Carbon steel elbow production process
The production process of carbon steel elbow manufacturers is basically hot pushing, stamping and medium plate welding. Hot pushing is generally used for the production of standard seamless pipes and straight seam pipe elbows.
The production speed is fast and the specifications and dimensions of the manufactured products are small.
This is the main advantage of the hot push process. The stamping process can produce thick-walled carbon steel elbows, which are suitable for small batch production.
How to distinguish elbow quality
Medium plate welding is generally used in the manufacture of large-diameter carbon steel elbows.
It can be processed in a wide range and is manufactured The elbows are relatively standard.
Country | Standard |
---|---|
United States | ASTM A234/A234M – Standard Specification for Piping Fittings of Wrought Carbon Steel and Alloy Steel for Moderate and High-Temperature Service |
European Union | EN 10253-1 – Butt-welding pipe fittings. Wrought carbon steel for general use and without specific inspection requirements |
Germany | DIN 2605 – Elbows and Bends with Reduced Pressure Factor |
Japan | JIS B2311 – Steel Butt-Welding Pipe Fittings for Ordinary Use |
China | GB/T 12459 – Steel Butt-Welding Seamless Pipe Fittings |
Russia | GOST 17375 – Carbon and Low-Alloy Steel Butt-Welding Fittings. General Specifications |
India | IS 1239 (Part 2) – Steel Tubes, Tubulars and Other Steel Fittings. Part 2: Steel Pipe Fittings – Elbow and Bend |
How to distinguish elbow quality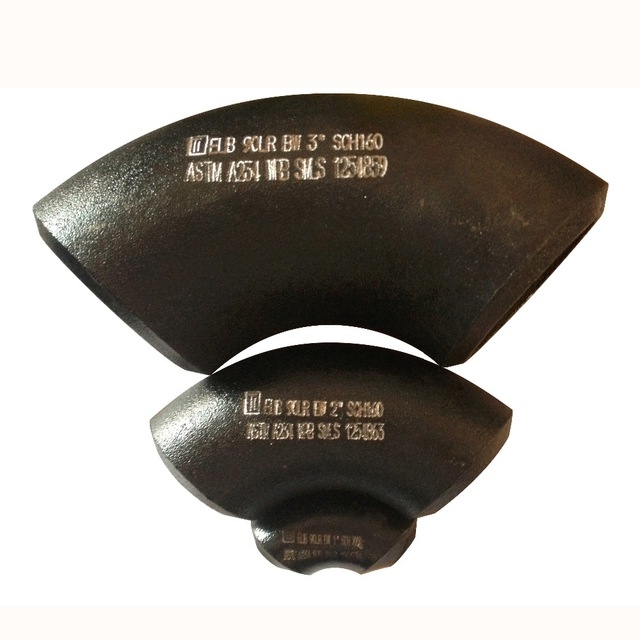
Distinguishing the quality of elbows involves assessing various factors related to their construction, material, and workmanship. Here are key indicators to differentiate between good and poor-quality elbows:
Material Quality:
Good Quality: High-quality elbows are made from premium materials such as ASTM A234 Grade WPB carbon steel, ensuring durability and resistance to corrosion.
Poor Quality: Inferior materials or a deviation from specified material grades can compromise the overall strength and longevity of the elbow.
Manufacturing Standards:
Good Quality: Elbows manufactured in adherence to recognized standards such as ASTM, EN, DIN, or other relevant industry standards exhibit consistent quality and reliability.
Poor Quality: Elbows that do not comply with established manufacturing standards may have inconsistencies in dimensions and mechanical properties.
Welding Quality:
Good Quality: Well-executed welding with smooth and uniform joints, free from defects such as cracks or incomplete fusion, is a sign of high-quality elbows.
Poor Quality: Poorly welded elbows may exhibit visual imperfections, irregularities, or structural weaknesses that can compromise integrity.
Surface Finish:
Good Quality: Elbows with a smooth and uniform surface finish, free from rust, scale, or other irregularities, indicate proper manufacturing and post-processing.
Poor Quality: Rough or uneven surfaces, signs of corrosion, or inadequate surface treatment can be indicative of lower-quality elbows.
Dimensional Accuracy:
Good Quality: Precise adherence to dimensional specifications, including diameter, radius, and wall thickness, ensures compatibility and proper fit within a piping system.
Poor Quality: Deviations from specified dimensions can lead to difficulties in installation and may indicate substandard manufacturing.
End Beveling:
Good Quality: Properly beveled ends, meeting industry standards, facilitate smooth welding and enhance the strength of the joint.
Poor Quality: Inadequate or inconsistent beveling may result in weak welds and compromise the overall structural integrity.
Certifications and Testing:
Good Quality: Elbows that come with relevant certifications and have undergone rigorous testing (such as visual inspection, radiographic testing, and mechanical property testing) demonstrate a commitment to quality control.
Poor Quality: Lack of certifications or evidence of comprehensive testing may raise concerns about the reliability of the elbow.
Reputation of Manufacturer:
Good Quality: Elbows produced by reputable and well-established manufacturers with a history of delivering high-quality products are more likely to meet industry standards.
Poor Quality: Elbows from less-known or unverified manufacturers may carry a higher risk of inconsistency and lower quality.
By carefully evaluating these factors, one can make informed decisions when selecting elbows for specific applications, ensuring they meet the required quality standards and contribute to the overall reliability of a piping system.