Detailed explanation of 316/316L stainless steel Slip-on flange technology
Slip on flange connection method
Comparison between Slip on flange and flat welding flange
The sliding sleeve flange uses flanges, steel rings, etc. to set the flange on the pipe end, and the flange can move on the pipe end.
The steel ring or flange is the sealing surface, and the function of the flange is to compress them.
Sliding sleeve flanges are suitable for the connection of steel, aluminum and other non-ferrous metals and stainless acid-resistant steel containers and corrosion-resistant pipelines.
The sliding sleeve flange is a movable flange piece, which is usually matched with water supply and drainage fittings.
When the manufacturer leaves the factory, there is a flange at both ends of the expansion joint, which is directly connected to the pipelines and equipment in the project with bolts.
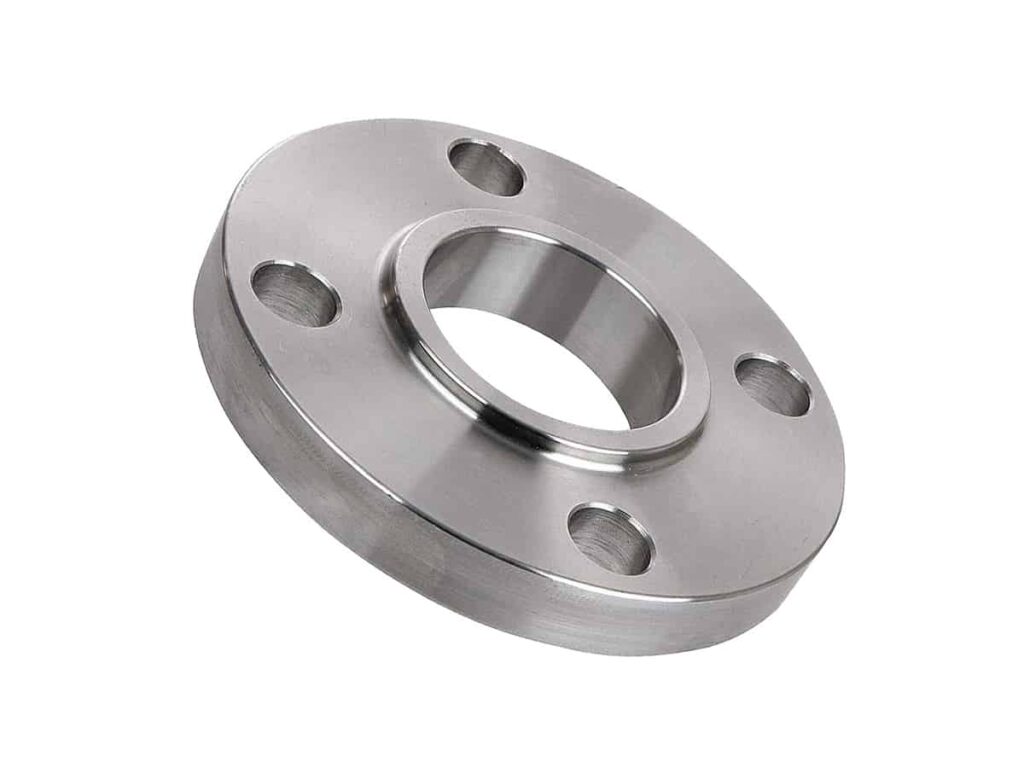
Slip on flange weld
The sliding sleeve flange welding method is to insert the steel pipe into the inner diameter of the flange and weld it.
Slip on flange Uses
Slip-on flange is often used in pipeline connections and conveying systems, and plays a very important role in the operation of machines.
It can connect pipelines and equipment of different specifications to ensure the tightness and reliability of pipeline connections and prevent liquid or gas leakage.
In addition, the slider flange allows for easy disassembly and replacement of equipment, making repairs and maintenance easier.
Slip-on flange is suitable for transporting various fluid media, including water, oil, gas, steam, etc.
It has the characteristics of simple structure, convenient connection, strong practicability and wide adaptability.
Widely used in machinery, chemical industry, shipbuilding, petroleum, electric power, metallurgy and many other fields.
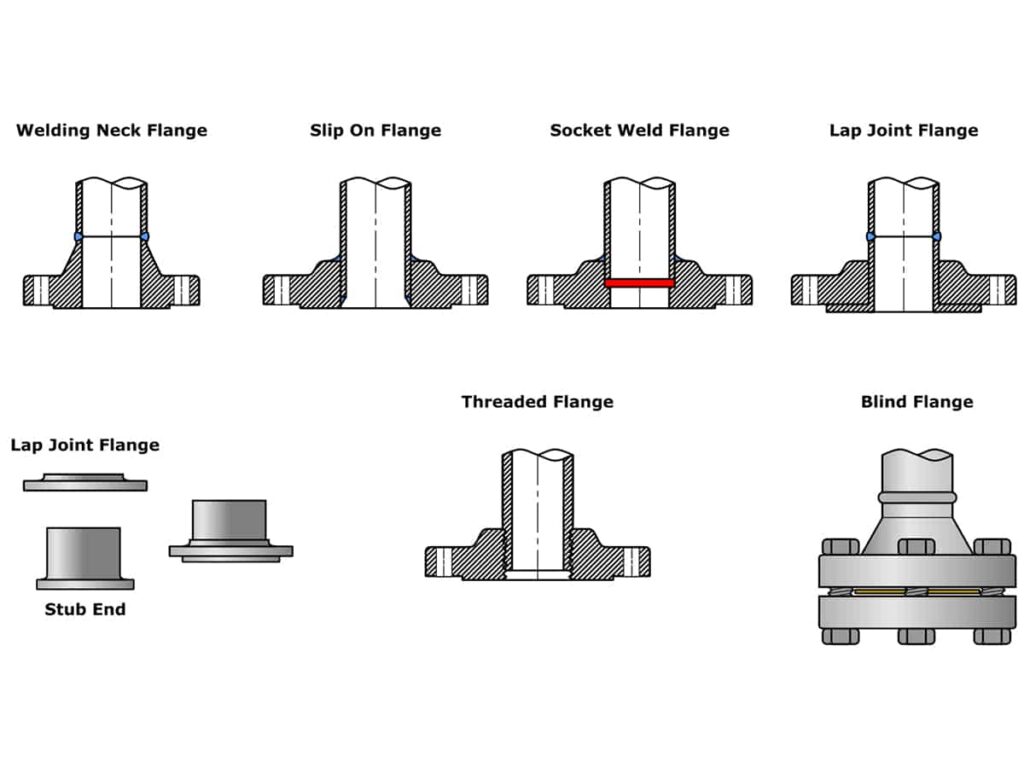
Slip on flange connection method
The sliding sleeve flange has certain grooves on the sleeve so that the flange can slide inside the sleeve and is then fixed with bolts.
Its structure is simple, just connect the pipes through sleeves and then tighten them with flange bolts.
The sliding sleeve flange realizes the connection and disassembly of pipes or equipment through the movement of the slide block.
When a pipe or equipment needs to be connected, the slider moves toward the center of the flange to connect the slider to the pipe or equipment.
Then, tighten the clamping nut to secure the connection between the slider and the flange.
When disassembly is required, the clamping nut is loosened and the slider can slide along the slideway to remove the pipe or equipment.
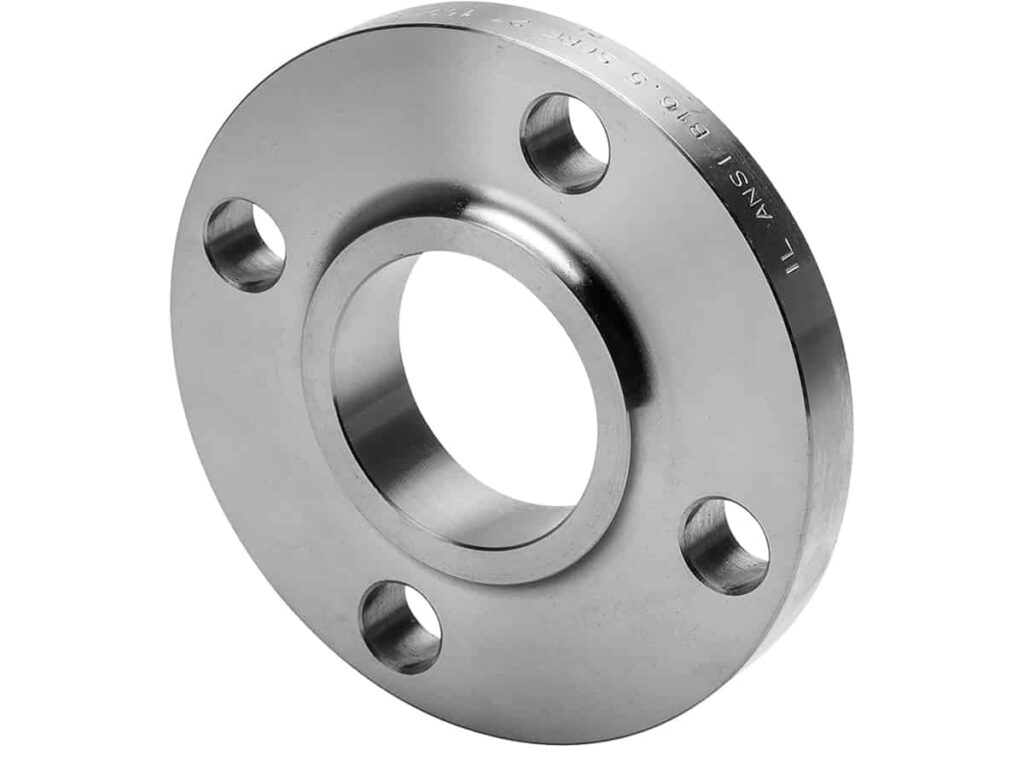
Comparison between Slip on flange and flat welding flange
Characteristic | Slip-On Flange | Flat Welding Flange |
---|---|---|
Connection Type | Slips over the pipe end and then is welded in place. | Welded directly to the pipe end. |
Flange Face Type | Flat face or raised face. | Typically flat face, but can be raised in some designs. |
Welding Process | Requires welding on both inside and outside. | Requires welding only on the outside. |
Ease of Installation | Generally easier to install due to slip-on feature. | Requires more precise alignment during welding. |
Strength and Integrity | Provides a strong and integral connection when properly welded. | Provides a strong connection but not as integral as slip-on. |
Surface Finish | Surface finish can be flat or raised, depending on the design. | Typically has a flat flange face for a consistent finish. |
Gasket Compatibility | Compatible with various gasket materials suitable for the specific flange face. | Compatible with gaskets suitable for flat flange faces. |
Applications | Commonly used in applications with lower pressure and temperature requirements. | Commonly used in various applications, including those with higher pressure and temperature requirements. |
Alignment and Precision | Easier to align due to the slip-on feature. | Requires more precise alignment during the welding process. |
Pressure Rating | Suitable for moderate pressure applications. | Can have high pressure ratings depending on design and materials. |
Common Standards | Conforms to standards such as ASME B16.5 or ASME B16.47. | Conforms to standards such as ASME B16.5 or ASME B16.47. |
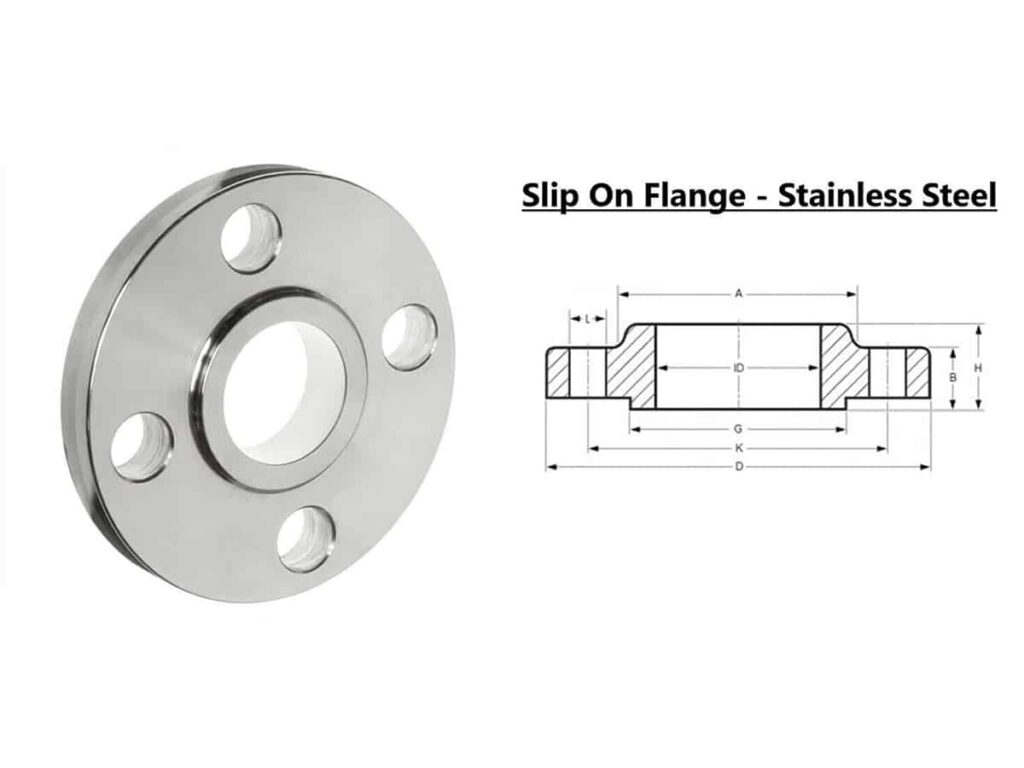
Slip on flange size
[Product material] 201, 304, 321, 304L, 316L, 310S, 2205, 904L and other carbon steel, stainless steel, alloy steel.
[Pressure level] 0.6Mpa~32Mpa, 150Lb~2500Lb, PN0.25~PN42.0, can be customized.
[Sliding sleeve flange standard] National standard, American standard, German standard, Japanese standard, British standard, etc., can be customized
National Standard】GB/T9122-2010
[American Standard] ANSI B16.5 Class150, 300, 600, 900, 1500 (WN, SO, BL, TH, LJ, SW)
[German Standard] DIN2573, 2572, 2631, 2576, 2632, 2633, 2543, 2634, 2545 (PL, SO, WN, BL, TH)
[Japanese Standard] JIS 5K, 10K, 16K, 20K (PL, SO, BL, WN, TH, SW)
[Pressure vessel standards] JB1157-82~JB1160-82, JB4700-2000~JB4707-2000 B16.47A/B B16.39 B16.48
[Sliding sleeve flange size] DN10MM-DN1828MM
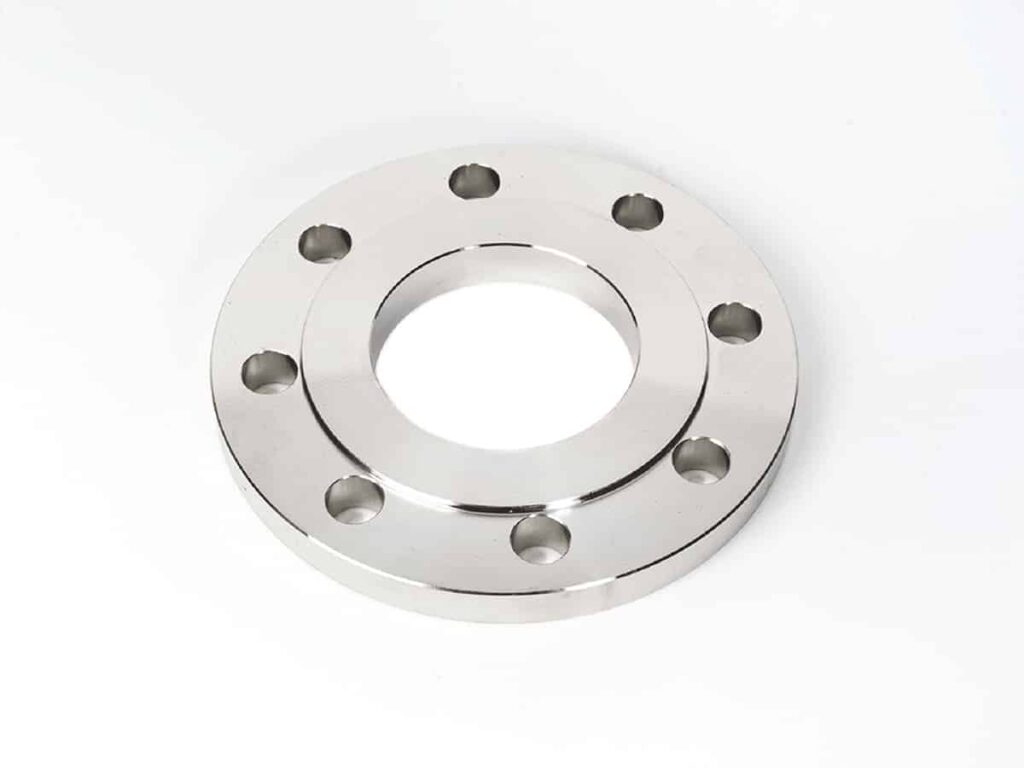