Do you understand the characteristics and specifications of butt welding flanges?
What is the use of weld neck flange?
What is the difference between weld neck and flange?
What are the disadvantages of a weld neck flange?
Butt welding flanges are generally made by forging or forging and rolling processes.
When made of steel plate or section steel, the following requirements must be met:
1. The butt welding flange should be ultrasonic tested and have no delamination defects;
2. It should be cut into strips along the rolling direction of the steel and bent butt welded into a ring. , so that the surface of the steel forms the cylindrical surface of the ring. Steel plates shall not be directly machined into necked butt welding flanges;
3. The butt welds of the rings shall be full penetration welds;
4. The butt welds of the rings shall be subjected to post-weld heat treatment and 100% radioactive or Ultrasonic flaw detection,
and radiographic flaw detection meets the Level II requirements of JB4730, and ultrasonic flaw detection meets the Level I requirements of JB4730.
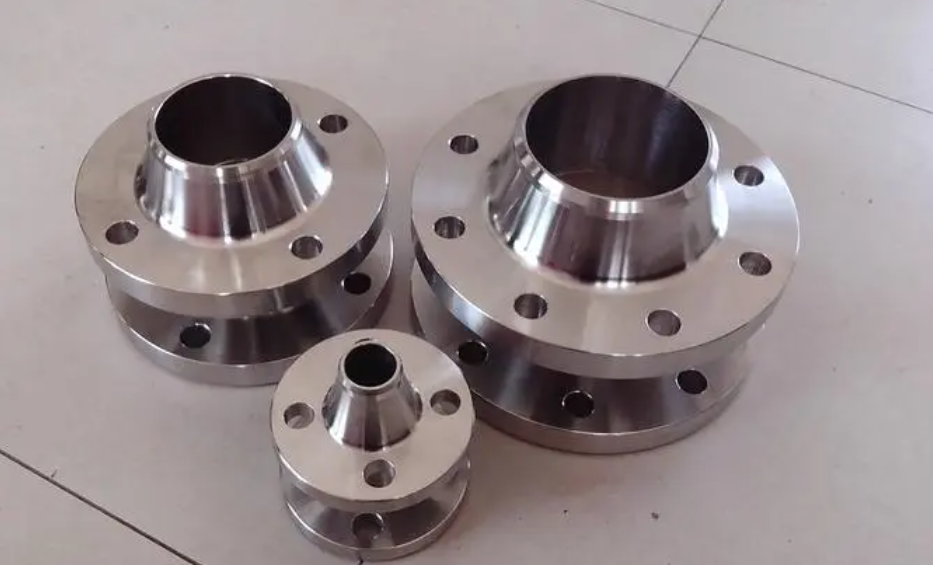
What is a weld neck flange?
Butt welding flange is a type of pipe fitting, which refers to a flange with a neck and a round pipe transition and is butt welded to the pipe.
What is the use of weld neck flange?
The butt welding flange is not easy to deform, is well sealed, and is widely used.
It has corresponding rigidity and elasticity requirements and a reasonable butt welding thinning transition.
The distance between the welding port and the joint surface is large, and the joint surface is protected from welding temperature deformation. It adopts a relatively complex method.
The trumpet-shaped structure is suitable for pipelines with large fluctuations in pressure or temperature or pipelines with high temperature, high pressure and low temperature.
It is generally used for the connection of pipelines and valves with PN greater than 2.5MPa; it is also used for transporting expensive, flammable and explosive materials. on the media pipeline.
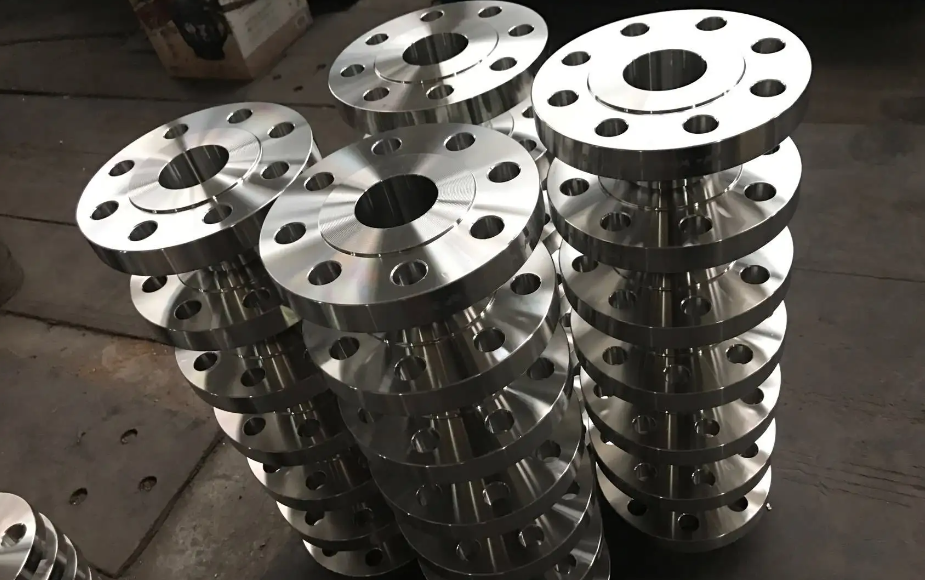
What is the difference between weld neck and flange?
Characteristic | Weld Neck Flange | Regular (Slip-On) Flange |
---|---|---|
Connection Type | Welded | Slip-on (also weldable) |
Design | Extended neck (hub) with a tapered bore for smooth flow | Flat face or raised face, no neck |
Strength | Generally stronger due to the extended neck providing additional support | Less robust compared to weld neck flanges |
Usage | Preferred in high-pressure and high-temperature applications | Commonly used in low-pressure and low-temperature applications |
Alignment | Requires precise alignment due to the extended neck | Easier to align during installation |
Cost | Typically more expensive due to the design complexity | Generally more cost-effective |
Applications | Petrochemical, oil and gas, chemical processing industries | Used in a variety of industries, especially for lower pressure systems |
Installation Difficulty | May be more challenging due to precise alignment requirements | Easier to install, especially in less critical applications |
Sealing Surface | Flat face or raised face for gasket sealing | Flat face or raised face for gasket sealing |
What are the disadvantages of a weld neck flange?
advantage:
(1) High strength: The butt welding flange has a high nominal pressure and can meet the connection needs of various high-pressure pipelines.
(2) Corrosion resistance: After heat treatment process, the butt welding flange has good corrosion resistance and can resist the erosion of various chemical substances.
(3) Good sealing: The butt welding connection method improves the sealing performance between the flange and the pipe and prevents medium leakage.
shortcoming:
(1) Higher cost: Compared with ordinary flanges, the production cost of butt welding flanges is higher, so cost and actual needs need to be considered when selecting.
(2) High installation requirements: Due to the special connection method of the butt welding flange, installation requires technology and equipment, and the requirements for installation personnel are high.
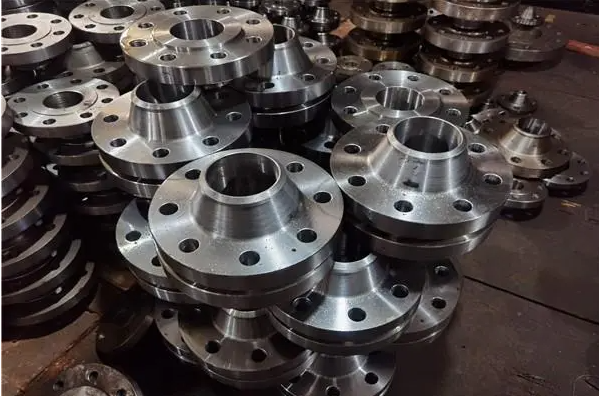
production materials
WCB (carbon steel), LCB (low temperature carbon steel), LC3 (3.5% nickel steel), WC5 (1.25% chromium 0.5% molybdenum steel),
WC9 (2.25% chromium), C5 (5% chromium % molybdenum), C12 ( 9% chromium 1% molybdenum),
CA6NM4 (12% chromium steel), CA15 (4) (12% chromium), CF8M (316 stainless steel), CF8C (347 stainless steel),
CF8 (304 stainless steel), CF3 (304L stainless steel), CF3M (316L stainless steel),
CN7M (alloy steel), M35-1 (Monel), N7M (Hastel B), CW6M (Hastel C), CY40 (Inconel)